LCD display displays a variety of images, how to make? chenchen takes you to understand the principle and production process
In today’s society, everyone is inseparable from a variety of electronic devices, especially computers and mobile phones, all kinds of videos, patterns and text in the devices are displayed through electronic screens, and the display devices of these electronic products are LCD screens. How does it display numbers or images? Then let’s understand the internal structure of the screen in detail and understand the principle.
First, the LCD screen structure
picture
LCD is short for liquid crystal display, and now the mainstream is TFT-LCD (thin film transistor-liquid crystal Display) technology.
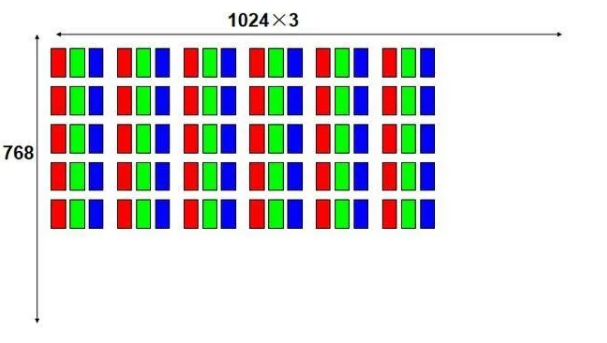
LCD display structure
Look at the disassembly of the above figure, the LCD screen should have a backlight, polarizer, and the most important thing is that the liquid crystal is placed in two parallel glass substrates, and the TFT thin film transistor is placed on the lower substrate, and the CF color filter is placed on the upper substrate (with RGB red, green and blue three-color light resistance).
Second, LCD screen color principle
picture
Because the CF color filter is printed with RGB three color blocks, then wait until the screen backlight light passes through, we look at the sequence compared to the following figure:
picture
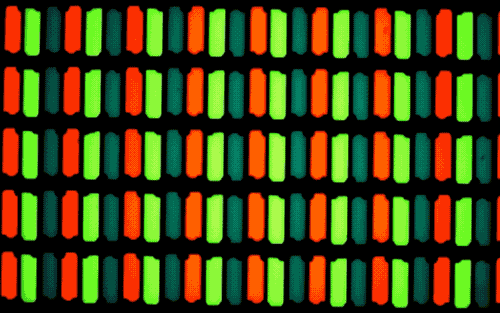
The light first passes through the transparent TFT thin film transistor substrate, and then through the liquid crystal molecules, and then through the CF color filter, under the influence of the different penetration rate of the liquid crystal molecules under the color block, the color block will emit the following bright and dark different red, green and blue three colors, so as to mix into the required color display.
picture
Of course, the premise is that this one color block should be small enough, small enough to form a rich color image, that is, we say pixels!
Taking a display with a resolution of 1024×768 pixels as an example, each pixel consists of sub-pixels of R, G, and B three primary colors, that is, a total of 1024×768×3 TFT transistors. As shown in the picture below:
picture
1024 x 768 resolution pixels
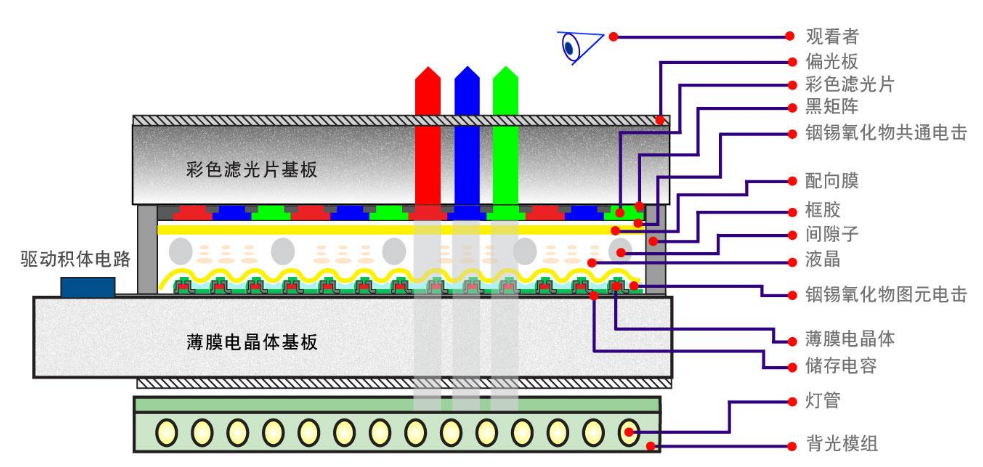
Liquid crystal module is a highly integrated electronic component, with excellent display effect, low power consumption, thin and portable characteristics, so it is widely used in various electronic products.
With the continuous progress of technology, the performance and function of liquid crystal modules are also constantly improving, and it has become an indispensable part of the modern electronics industry. Next, let’s take a look at the LCD module manufacturing process, because one production link is extremely accurate, almost all are closed processing, so the article uses the animated demonstration of GIFs.
Third, liquid crystal module production process
picture
The liquid crystal module production process refers to the process of assembling and processing the related parts and materials of the liquid crystal display. Liquid crystal module is generally composed of liquid crystal panel, backlight module, drive circuit board, etc. The following is a brief introduction to the production process of liquid crystal module.
First, prepare the LCD panel. Liquid crystal panel is the core component of liquid crystal display, which is composed of substrate, transparent electrode, liquid crystal material and so on. In the production process, it is first necessary to select the appropriate substrate material, and carry out chemical treatment and precision machining to prepare the substrate. Then, a transparent electrode is coated on the substrate to form a liquid crystal display electric field. Next, the liquid crystal material is filled between the substrate to form the liquid crystal layer. Finally, the upper and lower substrates are packaged together to form a liquid crystal panel.
picture
Above is the LCD LCD finished panel (Cell), anisotropic conductive adhesive (ACF), driver IC, flexible circuit board (FPC) and PCB circuit board using the machine together pressing.
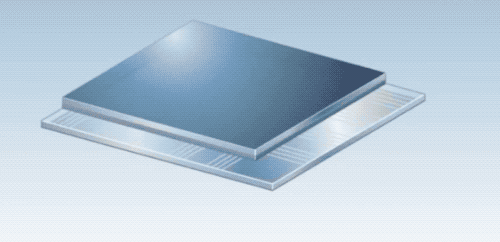
Secondly, the backlight module is prepared. The backlight module is responsible for providing the background light source of the LCD. The backlight module is generally composed of a light source, a light guide plate, a reflector and a lens. The light source can be cold cathode tube or LED. In the production process, the first need to select the appropriate light source, and assembly and testing. Then, the light radiated by the light source is converted and diffused through the optical guide plate, and finally through the reflection of the lens and the reflector, so that the light covers the entire liquid crystal panel.
picture
The above picture is assembled with the backlight plate, light source and iron frame.
Then, make the drive circuit board. The driver circuit board controls the LCD panel and the backlight module. In the production process, it is first necessary to design the layout and connection of the circuit board, and then solder components such as resistors, capacitors, and transistors to the circuit board. Next, test and debug the circuit board to ensure that it works properly.
Finally, the LCD module is assembled and tested. The LCD panel, backlight module and drive circuit board are assembled to form a complete LCD module. During the assembly process, precision tools and equipment are required to ensure the precise alignment and connection of individual components.
picture
After the assembly is completed, the liquid crystal module is tested, including brightness, color, contrast and other parameters, to ensure that its performance meets the requirements.
In summary, the production process of liquid crystal module includes preparing liquid crystal panel, preparing backlight module, making drive circuit board and assembling and testing liquid crystal module. These steps require precise process control and professional equipment to ensure that the quality and performance of the LCD module meet the requirements.
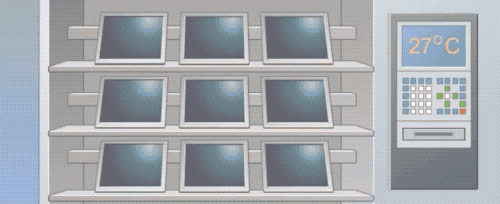
What is the meaning of the LCD module production process?
The LCD module has a set of standardized production process, which can not only clearly distinguish whether the product is qualified, but also the effective guarantee of the company’s product quality and shipment rate, and can improve production efficiency and save costs.